





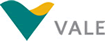

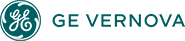






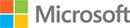
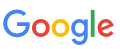

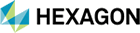


In the west of Singapore, less than 10 miles separates the Tuas Biomedical Park, which is home to manufacturing plants run by Big Pharma companies like GlaxoSmithKline and Pfizer, from Biopolis, the research and development complex for biomedical sciences, where basic drug discovery, clinical development and medical technology research all take place. Yet when it comes to connecting the two worlds of the R&D lab and the manufacturing plant to take research innovations into large-scale production, that distance can often seem a lot longer.
For Emerson, which rather neatly has its Asia Pacific HQ located almost in the middle between these two life sciences industry sites, it has traditionally gravitated towards the Tuas Biomedical Park to deploy technology, such as the DeltaV control system and DeltaV manufacturing execution system (formerly known as the Syncade MES) in pharma and biopharma production plants. Indeed, as ChowYang Neo, Senior Director of Marketing & Planning, pointed out at the start of the Emerson Life Sciences Innovation Seminar 2024, 80 percent of life sciences manufacturing capacity in Singapore is powered by Emerson’s DCS and MES technologies.
But from its comfortable position on the pharma factory floor, Emerson is increasingly looking upstream to the more rarified world of R&D, especially since the 2022 acquisition of AspenTech and the arrival of a whole new suite of solutions. And no doubt deliberately, the company chose Biopolis as the venue for this seminar, with a view to attracting scientists working in the R&D hub to hear and learn about solutions that can serve all the key stages of Discovery. PreClinical, Clinical Trials, Regulatory, and Production. Of particular emphasis was how Emerson is enabling pipeline acceleration i.e. getting products from the lab to the plant much faster to meet burgeoning and often urgent demand for new innovative therapies.
Flying in from California to be keynote speaker at the seminar was Emerson’s David Zhang, Vice President of Scheduling and PLM Solutions. He later sat down with ARC Advisory Group to talk about exactly how Emerson is working to automate and alleviate the onerous manual transfers of technology between life sciences stages. The interview follows below.
ARC: Could you describe your current portfolio responsibilities and working history at Emerson?
I am Vice President of Scheduling and PLM solutions within Emerson’s industrial software business that was created about 18 months ago and comprises the entire portfolio from the AspenTech acquisition as well as homegrown Emerson industrial software platforms. I am responsible for two key software solutions: Real Time Modeling System and Process and Knowledge Management (PKM)
I actually came to Emerson through another acquisition – Bio-G in 2019. I co-founded that company in 2008, and we became the market leader in finite scheduling and discrete event simulation for the life sciences industry. How? By doing away with paper records and manual scheduling, we revolutionized the industry in much the same way GPS revolutionized travel by eliminating maps and manual plotting of routes.
The Real Time Modeling System, originally developed at Bio-G, allows customers to produce more out of their facilities through debottlenecking and capacity analysis. Using the same simulation model, users can turn on a real-time scheduling capability. The biggest problem with a schedule is keeping it up to date, and that’s where we connect into the control systems, using process data as a real-time source of information and ensuring minimal loss of information from engineering intent to manufacturing reality.
ARC: And for Process & Knowledge Management (PKM), what problem does this look to solve for life sciences customers?
Essentially, PKM, which became part of the Emerson life sciences portfolio after the 2022 acquisition of Fluxa, tackles the issue of technology transfer. When a company is making a new drug, it has to figure out which facility is going to manufacture it. If the drug is still in clinical trials, then you only need small volumes, but when you want to commercialize, you need much larger volumes and a much bigger facility. Technology transfer has always been a major problem within the life sciences industry as there are many considerations, including manufacturing capability, IP protection, licensing, regulatory, etc. Each step of the tech transfer process adds significant time, reducing speed to market.
Consider this – for a single technology transfer for a single product into a facility, there are up to 10,000 parameters that need to be modified. Scale that across an entire product life cycle, and you’re looking at many tens of thousands of parameters. Across an entire product portfolio, hundreds of thousands.
What PKM does is provide a structured central repository for drug development information, recipes, and manufacturing processes, which helps to eliminate siloed data. Across R&D and manufacturing, information is captured and standardized digitally. Users at every stage of the pipeline have fast, intuitive access to this data, making the tech transfer process much simpler and quicker.
ARC: The One-Click Technology Transfer initiative – what exactly is that?
What I just talked about with PKM refers to a single company’s operations, i.e. companies like Roche that do both the R&D and the manufacturing themselves, and we’ve proven that “one-click” technology transfer within an organization is possible. But in the life sciences ecosystem you have many other companies doing perhaps only contract R&D or only contract manufacturing, and we want to simplify that tech transfer externally between different partners in the same way we can do it internally for companies like Roche.
To that end, in October last year, we announced the One-Click Technology Transfer Board, an executive panel comprising Emerson customers FUJIFILM Diosynth Biotechnologies, Merck, and Pfizer, which will lead the development of strategies, solutions, and guidelines to convert today’s life sciences manufacturing recipe transfer process into a digitalized production platform and help speed life-saving drugs to market.
It’s a major, long-term project for us, but the holy grail is to have therapies producible anywhere in the world and at low cost. Much like the logistics industry is completely streamlined, drug manufacturing is also capable of doing so and we want to be at the center of it.
ARC: I understand that there is a Singapore aspect to the One-Click initiative?
That’s correct. Being home to 8 of the world’s top 10 life sciences companies, plus the fact that 80 percent of life science capacity here is already powered by our DeltaV control system and DeltaV MES, means Singapore is a very important place for Emerson. To progress the One-Click Technology Transfer initiative, with support from the Singapore Economic Development Board (EDB), we have opened a dedicated research center at the Tuas Biomedical Park to design, develop and verify the software and digitalized production platform necessary to enable the external technology transfers that will be so beneficial for the industry. In Singapore, for Emerson, having customers right here in our backyard enables a lot of quick testing and getting a One-Click solution to the market faster.
ARC: Finally, what are some of the key trends across the life sciences industry you’re seeing?
Life sciences is a rapidly changing environment with many new advancements today that could only be imagined a few years back. Take, for example, the rapidly expanding ATMP (Advanced Therapy Medicinal Products) space where we are treating the root cause of disease using gene therapy instead of just managing the symptoms. Personalized medicines have the potential to increase the efficacy of a therapeutic and introduce a completely new paradigm of manufacture where the necessity is to scale-out capacity instead of scale-up.
This trend is important for automation companies like Emerson, which traditionally serve facilities with large sets of process equipment making large quantities of drugs for large numbers of people. But with personalization, where you’re effectively producing for just one patient, it becomes totally different. You don't need all this big equipment anymore.
And there's always something new around the corner in this industry. Who could have foreseen, for example, that that a drug developed for diabetes, Ozempic, could become a cure for obesity and the next big blockbuster? So yes, life sciences is really a fascinating place to be in right now!