





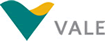

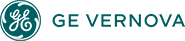






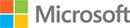
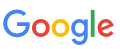

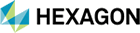


Multiple technologies have emerged in recent years that are instrumental in driving the advancement of smart manufacturing and the Industrial IoT. These include advanced analytics, artificial intelligence (AI) and machine-learning (ML), operational intelligence, advanced robotics, cyber-physical systems, and generative design for additive manufacturing. While each of these technologies is changing the face of manufacturing today, ARC Advisory Group research suggests that the Industrial IoT, connected smart assets, and especially the Digital Twin are having the most immediate and significant impact on how companies implement technologies that enable smart manufacturing.
The basic concepts surrounding the digital twin have been defined, frameworks established, and continue to evolve due to technological advancements and more clearly defined business goals. The benefits have been evaluated and validated and industries are now moving into the implementation phase.
Today, production engineers are merging virtual engineering models with the physical equipment in an environment that allows for operational performance improvement as well as predictive maintenance of the equipment. Moreover, due to the advancement and evolution of enabling technologies like virtual simulation modeling and digital twin development platforms, we see renewed focus on the implementation of the digital twin and associated benefits that could be gained. Using digital twins that represent the product and production systems, manufacturers can reduce the time and cost associated with assembling, installing, and validating factory production systems. Additionally, implementing digital twins for asset management typically provides quantifiable benefits for maintaining equipment in the field.
An integral component of a digital twin of production system is the virtual model of the real-world products, assets, and processes. Virtual modeling provides manufacturing engineers with the ability to simulate and model both the virtual and the physical, simultaneously or separately. This digital twin system modeling approach enables them to understand the holistic nature of their assets and production systems within the overall manufacturing ecosystem. Further, we are seeing the emergence of powerful digital twin development tools offered by suppliers that will enable manufacturers to understand exactly how their factory systems and equipment function and enable them to make decisions to enhance performance and product quality through human and artificial intelligence.
Digital twins can be applied to discrete manufacturing ecosystems in three distinct areas: product, production, and performance.
The product digital twin is used to enable more efficient design, and to improve the product. In some cases, the product is the actual equipment and assets used in the production system. Virtual simulation modeling can validate product performance, while simulating how the product is currently behaving in a physical environment. This provides the product developer with a physical-virtual connection that allows them to analyze how a product performs under various conditions and make changes in the virtual design model to ensure that the physical product will perform as designed in the field. This eliminates the need for physical prototypes and reduces development time.
Production digital twins are used in manufacturing and production planning. They can help to validate how well a manufacturing process will perform on the shop floor before the physical production equipment and work cells go into actual production. Today, the virtual commissioning of production automation - an established technology and process - is merging with the more expansive scope of the digital twin. Virtual commissioning is typically a one-time validation of an automated production system. In contrast, the digital twin represents an ongoing analytical and optimizing process that takes place in real time. By simulating the production process using a digital twin and analyzing the physical events across the digital thread, manufacturers can create a production environment that remains efficient under variable conditions.
Performance digital twins are used to capture, analyze, and act on operational data. An important initial step when developing and implementing a digital twin is to identify the exact operational configuration of the product, asset, or production equipment that represent the physical components. When implementing, companies need to include context within the digital twin configuration. For predictive analytics or Industrial IoT to be effective, the context (physical configuration) of the asset and system are required to know exactly what is needed to collect the relevant operational and performance data. Companies implementing any digital twin project should begin by capturing and managing the actual physical configuration of the asset.
ARC Advisory Group clients can view the complete report at ARC Client Portal
If you would like to buy this report or obtain information about how to become a client, please Contact Us
Keywords: Digital Twin, Smart Manufacturing, Industrial IoT, Operational Intelligence, Context, Cyber-physical Systems, Interoperability, Model-based Systems, ARC Advisory Group.